Construction Blog
Fastening advices for experts
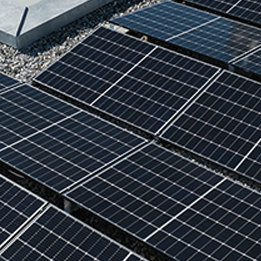
Pitched roof or flat roof? What fastening options are available? – Solar Guidebook Part 3
In the third part of our solar guidebook we use two installation examples to show the various options for fastening solar systems on pitched roofs and flat roofs and provide information on what needs to be taken into account.